Variable speed compressors can save up to 30% of energy used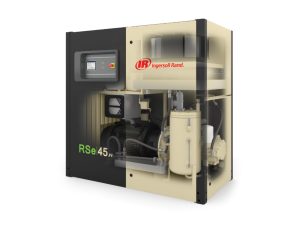
With the huge developments of electronics and control systems over the past 20 years or so, the compressed air industry been able to introduce wide range of energy efficient variable speed compressors. To understand where the energy saving achieved by running a variable speed compressor comes from, you need to understand where the in-efficiencies come from in fixed speed units.
How do fixed speed compressors operate
Fixed speed compressors operate, as the name suggests, at a standard fixed speed. Regardless of how much air you need or are using at any moment the compressor is either:
- running at full speed,
- running at full speed in an intermediate condition or ‘unloaded’
- not running at all
When running at full speed the compressor is making the full designed amount of compressed air. When not running it doesn’t make any air. The intermediate stage ‘running unloaded’ is where the compressor is turning at full speed but not making any compressed air. This unloaded running is designed to keep the compressor turning at full speed so it can quickly start to make more compressed air if demand suddenly returns. This is unloaded running is required because electric motors are limited in the number of starts they can make every hour.
A typical fixed speed air compressor will start up, it will produce compressed air as it fills up the compressed air system and receiver vessel. Once maximum pressure is reached, the compressor will run unloaded for a period of several minutes before shutting down completely and stopping. If air demand returns (ie system pressure drops) whilst the compressor running in an unloaded condition it will immediately start making compressed air again. If air demand returns when the compressor has stopped, the compressor will restart from stationary and start making compressed air again.
The downside of running un-loaded is that the compressor is using up to 50% of the design energy but isn’t making any compressed air. Effectively, during the running unloaded period, the compressor is using energy but not producing anything, this energy is totally wasted.
How are variable speed compressors different to fixed speed compressors?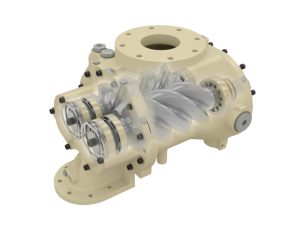
Variable speed compressors operate in a different way to fixed speed units. Variable speed compressors regulate the speed they turn at so the amount of air they make exactly matches demand. As the air demand falls, the compressor speed reduces, so the compressor makes less air. As the air demand increases the compressor speed increases, so the compressor makes more air. When the variable speed compressor slows down there is an approximately proportionate reduction in energy usage.
There are of course limitations. The maximum amount of air the compressor can make occurs when it is turning at 100% rated speed. At this point it is effectively operating as a similar sized fixed speed machine. At the bottom end the compressor can typically turn down to a minimum of about 30% of rated speed. Below this the compressor stops.
The downside of variable speed compressors is that the controls and electronics required to enable the motor / compressor to run at different speeds is very expensive. Typically variable speed compressors can be around 30% more expensive than a fixed speed unit of the same size.
Do they save you energy in all circumstances?
Variable speed compressors can save significant amounts of energy under the right circumstances. If you have a production line where the air demand is very stable a correctly sized fixed speed compressor will be very efficient and a variable speed compressor wont save you much. However, if you air demand is very variable, eg dropping to around 50% for a period and then back up to 100% for a time regularly, or if you run a skeleton staff at night and a full staff during the day, then the variable speed machine can save you over 30% of the energy used to create the compressed air.
To find out more about variable speed compressors call us on 01480 217904 or contact us